Как делают автобусы: экскурсия по заводу MAN в Анкаре - «MAN»
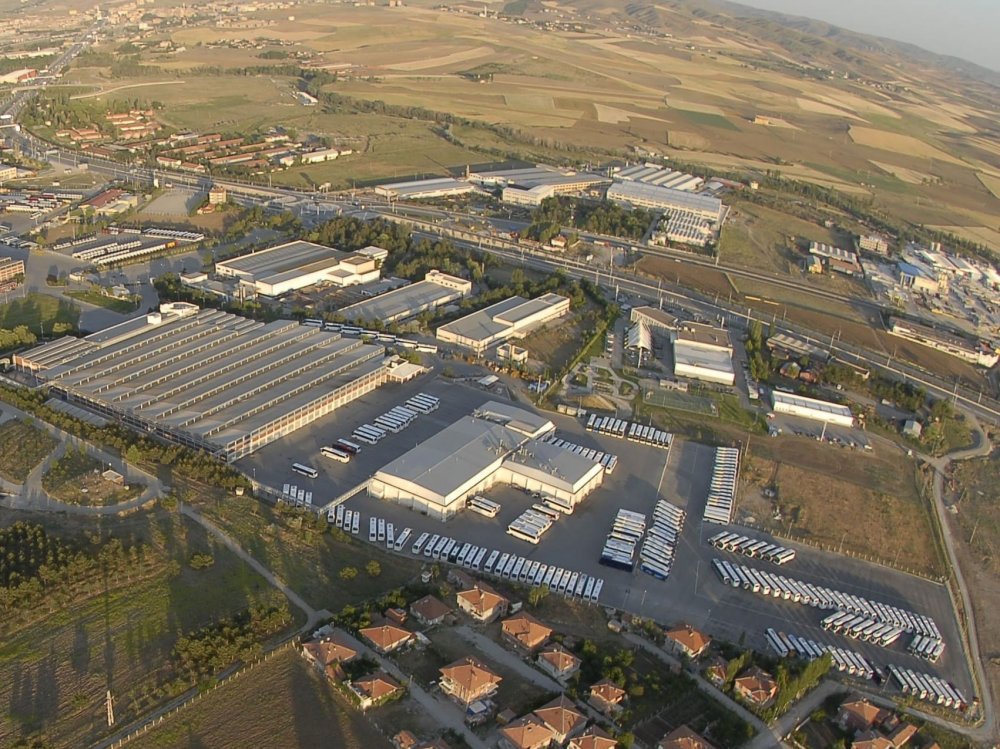
Фраза «Кто видел один современный автомобильный завод – видел их все» давно стала общим местом, затертым трюизмом… Каюсь – и я ее написал не один раз. Казалось бы, завод, на котором делают автобусы, ничем не должен отличаться от заводов, на которых делают легковушки. Ведь что такое автобус? Тот же пассажирский автомобиль, только большой. Но, как оказалось, размер имеет значение…
В том, что производство автобусов совершенно не похоже на производство легковых автомобилей, я убедился, когда мне довелось посетить завод концерна MAN в Анкаре. Мало кто назовет Турцию в числе великих автомобильных держав. Действительно, собственных турецких марок немного, да и те, что существуют, например, Отокар и Ашкам, в основном поставляют продукцию исключительно на внутренний рынок.
Вместе с тем, в Турции действует множество заводов, принадлежащих совместным предприятиям с мировыми автомобильными концернами. В 2019 году в этой стране было произведено 1 462 000 автомобилей, в том числе 479 000 коммерческих и 983 000 легковых, что позволило Турции войти в число 15 крупнейших стран-автопроизводителей мира и пятерку лидеров по производству автомобилей в Европе. При этом Турция – крупнейший в Европе производитель автокомпонентов, 75% произведенных транспортных средств экспортируется, и продукция автопрома составляет порядка 16% турецкого экспорта. Здесь производят автомобили под марками Renault, Fiat, Toyota, Mercedes, Isuzu… Завод по производству автобусов компании MAN занимает среди этих предприятий весьма заметное место.
Это история началась в 1966 году, когда в Стамбуле был заложен завод по производству грузовиков MAN, и уже в следующем году с его конвейера сошел первый автомобиль. В 1968-м там был собран первый автобус, в 1969-м на заводе освоили самостоятельную сварку кабин. Производство набирало обороты, однако для того чтобы отправить первый произведенный в Турции грузовик на экспорт, понадобилось 12 лет.
В 1985 году было решено, что велик Стамбул, но производству там тесновато, и есть необходимость организовать вторую площадку. В общем, в том же году завод по производству грузовиков и двигателей в Анкаре дал первую продукцию, а в 1995-м было принято решение продать предприятие в Стамбуле и сосредоточить производство в столице. Следующим шагом стало решение полностью сосредоточиться на производстве автобусов, и на сегодня завод – самый крупный из автобусных заводов MAN.
Здесь делают всю линейку моделей – и городские Lion’s City, и междугородные Lion's Intercity, и туристические Lions Coach, и роскошные автобусы марки Neoplan: Skyliner, Cityliner и Tourliner. Кстати, это единственный завод, где производят автобусы Neoplan.
Ну а теперь о самом заводе…
Первое впечатление – он огромен: 317 200 кв.м – это не шутки, и масштабы промплощадки хорошо видны на любезно предоставленной пресс-службой завода фотографии, сделанной с высоты птичьего полета. Попасть на эту территорию очень непросто – охрана на въезде производит весьма серьезное впечатление. Не расслабленная вохра «с огурцом в кобуре», а такие собранные суровые парни в бронежилетах, вооруженные штурмовыми винтовками. Нас, конечно, не досматривали и даже документов не проверяли. Разгрузили около административного корпуса, завели в конференц-зал, выдали бейджи с разноцветными наклейками и отправили на экскурсию. И мы буквально сразу убедились в том, что производство автобусов совершенно не походит на производство легковых машин. Современные автомобильные производства поражают малолюдьем и обилием роботов. Здесь же – настоящий муравейник, а вот роботов я не видел ни одного. Может быть, на каких-то участках они и используются, но отвечают они в таком случае лишь за какие-то вспомогательные операции. Основное делают люди.
В целом мне показалось, что организация производственного процесса больше напоминает авиазаводы или судоверфи. Начинается все с производства несущего каркаса, силовой клетки, на которую затем будут навешаны все агрегаты будущего дорожного лайнера. И в начале процесса этот силовой каркас выглядит как штабеля разнообразных металлических профилей, в основном – труб квадратного сечения, частично прямых, частично – слегка изогнутых.
Первый этап сборки – все необходимые элементы размещаются на кондукторах оснастки, которые и свариваются вместе в шесть блоков: передний, задний, верхний, нижний и два боковых. Используется только ручная сварка, а для подгонки по месту применяется простой и эффективный инструмент типа «кувалда». Первые проверки геометрии – и все шесть блоков соединяются на стапеле-кондукторе в единый каркас. И вновь в ход идут молотки, кувалды и сварочные аппараты. Затем борта зашиваются предварительно раскроенными листами металла толщиной 1 мм, и каркас, в котором уже угадывается облик будущего автобуса, вновь проходит проверку на геометрию. И если все нормально, то каркас поступает в цех катафорезной грунтовки.
Надежная антикоррозионная защита несущей конструкции транспортного средства – залог его долголетия, а срок эксплуатации автобусов, особенно автобусов категории «люкс», достаточно долог. Поэтому катафорезная грунтовка, которая на порядок эффективнее оцинковки, и была выбрана в качестве такой меры защиты. Физический смысл процесса таков: деталь, на которую наносится грунт, помещается в ванну с раствором. К ней подключается анод, а к корпусу ванной – катод, который активирует растворенные частички грунта положительными зарядами. В результате электролитической реакции положительно заряженные частицы закрепляются на отрицательно заряженном металле. Естественно, перед этим с детали должна быть удалена оксидная пленка, и она должна быть обезжирена. Но представьте, что «деталь» – это каркас автобуса длиной 12-13 метров! И ванночки, в которых ее предстоит искупать, должны иметь соответствующие размеры, и заботливые руки, которые будут окунать деталь в эти ванночки, должны иметь соответствующую мощность. В общем, катафорезный цех представляет собой череду таких ванн, в которых каркас проходит обезжиривание, фосфатирование и непосредственно процесс катафорезной обработки. Ну а между ними расположены ванны, в которых осуществляется промывка. Наконец, обработанный каркас автобуса отправляется в сушильную камеру, на окраску и – на участки, где и происходит окончательная сборка.
Прошлись мы и по этим участкам. Катафорезный цех оказался самым безлюдным, а здесь – много ручного и очень квалифицированного труда и никаких роботов. Правда, труд серьезно облегчают многочисленные средства малой механизации. Как, например, без них с ювелирной точностью вклеить огромное лобовое стекло туристического автобуса? И, естественно, монтаж интерьеров, электрического и электронного оборудования осуществляется исключительно вручную. А как иначе?
Есть и еще один фактор. На заводе параллельно собираются и городские автобусы, включая новейшую модель L4C, и междугородные, и туристические. Конструктивно они различаются весьма серьезно, при этом то, какие именно модели, в каких вариантах и в каком количестве будут производиться, определяется конкретной конъюнктурой заказов. И если городские или междугородные автобусы все-таки производятся сериями, состоящими из более или менее одинаковых машин (например, недавно завод поставил «Мосгортрансу» 150 автобусов), то туристические и экскурсионные автобусы категории «люкс» производятся практически по индивидуальным спецификациям.
Все это вместе приводит к высокой востребованности ручного труда, что, в свою очередь, отражается на численности рабочих. Даже с одного участка на другой кузова автобусов перекатываются вручную! На сегодняшний день на предприятии работает 2923 человека, из которых производственный персонал – 2238. Остальные работают в офисе, в обслуживающих структурах (рабочих, например, нужно кормить) и в НИОКР. Но завод постоянно наращивает мощность, и к концу 2020 года численность работающих достигнет 3380 человек. Уже сегодня предприятие работает в две смены, доведя производственный такт до 16 автобусов в день, 9 в первую смену и 7 – во вторую. А еще пять лет назад ежедневная производительность завода была вдвое меньше... При этом на производство одного автобуса, со времени его закладки и до того момента, когда готовый, сверкающий свежим лаком автобус выкатывается из ворот и отправляется на площадку готовой продукции, уходит почти месяц!
Ну а в целом экскурсия получилась очень познавательной. Оказывается, предприятие, способное выпускать ультрасовременную и при этом вполне конкурентную продукцию, не обязательно подразумевает шеренги промышленных роботов и беспилотных тележек, доставляющих детали с автоматизированного склада. Оно вполне может быть и таким, как завод автобусов MAN в Анкаре…


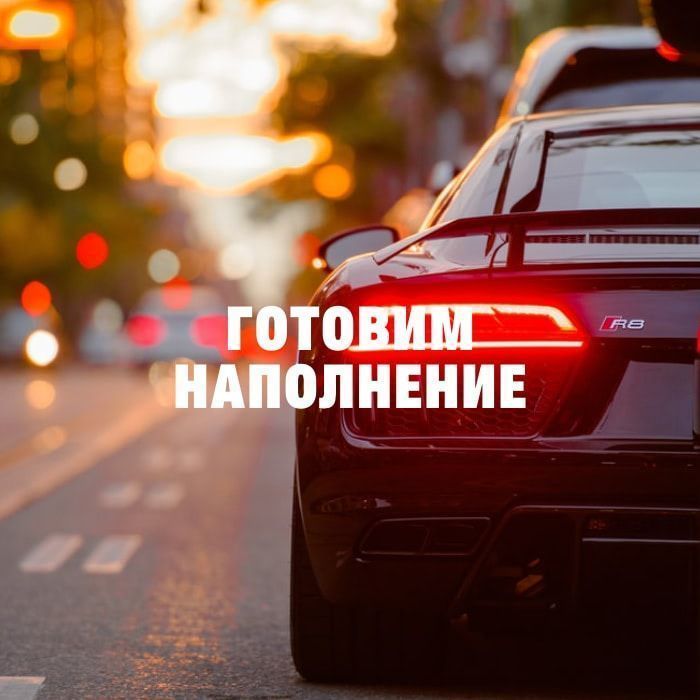
